Экскурсия по томскому заводу резиновой обуви
От ботинок «прощай молодость» и азиатских галош до обуви в индустриальном стиле
В прошлом году Томскому заводу резиновой обуви исполнилось 80 лет: если в 50-х годах прошлого века предприятие прославилось своими фирменными клееными галошами, то сейчас здесь производят обувь как под собственной торговой маркой HARWELD для охоты, рыбалки и активного отдыха, так и высокотехнологичную обувь, связанную с различными рисками на производстве.
Для того чтобы узнать, как обстоят дела ТЗРО сейчас, на предприятие прибыла редактор сайта «Сибирь работает» Анастасия Гнедчик.
Ультрамодные галоши с красной подкладкой и ботинки «прощай молодость»: краткий экскурс в историю завода
Как театр начинается с вешалки, так завод — с проходной. И здесь нас встречает Татьяна Кулакова, председатель профкома предприятия, проработавшая на заводе 45 лет.
Татьяна Николаевна провела нам краткий экскурс в историю предприятия. И тут есть чем поделиться:
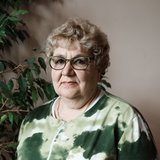
Томский завод резиновой обуви основали в 1942 году на базе эвакуированного из Москвы завода «Красный богатырь». Разместили предприятие в центре города, в неприспособленных помещениях, и всё это пространство нужно было освоить, а разукомплектованное оборудование — собрать.
— Октябрь-ноябрь, начало морозов, а сотрудники (их на тот момент было около 50) прибыли семьями, и все вместе собирали оборудование, чтобы начать работать. Стартовали с выпуска продукции для нужд армии: противогазов, резины для танков, амортизаторов для самолетов и защитных резиновых перчаток.
Уже в 1944 году завод начал выпускать обувь для гражданских: сначала — первые клееные галоши, затем — «праздничные» среднеазиатские галоши с красной подкладкой и специальные — для женских туфель; ботинки «прощай молодость» и резиновые сапожки. Среднесуточный выпуск галош в то время составлял 400-800 пар.
— В Советское время (в 70х-80х годах) завод входил в тройку крупнейших предприятий в отрасли. Завод переехал из центра Томска (из неприспособленных помещений) на новую промплощадку, спроектированную специально под него.
Было закуплено зарубежное оборудование, позволяющее выпускать обувь из пенополиуретана. Налажен выпуск обуви специального назначения (шахтерские, кислотощелочестойкие и рыбацкие сапоги), садовые и клееные лакированные галоши восточных фасонов; литьевые сапоги, сапожки и прогулочную обувь из ПВХ, а также резинотехнические изделия и сырые резиновые смеси.
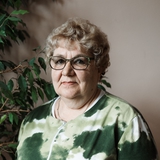
В 90-х, как и вся страна, завод столкнулся с разными проблемами. Инфляция, долги, низкая покупательская способность привели к резкому сокращению объема выпускаемой продукции, и как следствие, сокращению штата завода. Однако коллектив завода выдержал все испытания, и в нулевых завод начал закупать новое оборудование и создавать новый ассортимент выпускаемой продукции.
А что с заводом сейчас?
Известно, что на данный момент ТЗРО полон планов и активно развивается: утверждена долгосрочная поэтапная программа модернизации на предприятии. На заводе устанавливают изготовленное по заказу современное высокотехнологичное оборудование, модернизируют и расширяют линейку выпускаемой продукции и увеличивают каналы сбыта. Нам же провели по заводу потрясающую экскурсию.
Место, где из идеи рождаются наброски и эскизы будущей обуви
Начинаем с модельно-конструкторского отдела — здесь появляются наброски и эскизы. После множества изысканий и доработок появляются опытные образцы обуви.
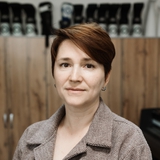
Мы разрабатываем обувь с нуля: сами создаем эскизы моделей, печатаем прототипы (3D-модели), сканируем их, а затем отливаем колодки из алюминия и изготавливаем изделия из резины, полиуретана, ЭВА и ПВХ, проектируя собственные лекала. Процесс это сложный, нужно учесть множество нюансов — от процента усадки пластика и алюминия до правильного построения стопы, чтобы человеку было удобно в нашей обуви ходить.
— Для правильного проектирования колодки и ее реализации уходят месяцы, а цикл производства с нуля — от момента, когда мы утверждаем эскиз, до выпуска первой партии обуви, — занимает около года.
Перед финальным выпуском опытные образцы изделия отдаем на пробную носку предприятиям, которые будут эксплуатировать эту обувь
— По итогам эксплуатации вносим коррективы, сертифицируем и запускаем ее в производство. А часть образцов повседневной обуви тестируют сами сотрудники.
Собственная лаборатория ТЗРО
Поскольку на заводе реализован полный цикл производства, то и проверяют партии сырья и материалов перед запуском в собственной испытательной лаборатории.
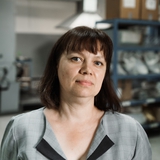
Сырье, которое приходит к нам на завод, проходит контроль в том числе и на соответствие ГОСТам — мы сами всё проверяем. Готовую продукцию мы тоже инспектируем на хрупкость, выдержку температур, истираемость подошвы, силу удара носка и другие технические условия. За качество всей продукции мы отвечаем.
Оборудование — резиносмеситель, пресс, вальцовочный станок и другое — в лаборатории, по заверению Елены Ковалевской, сертифицировано и надежно, постоянно диагностируется и ремонтируется.
А недавно лаборатория начала получать новое современное оборудование, которое позволяет производить дополнительный набор испытаний.
А как обувь производится?
Процесс создания резиновой обуви начинается с цеха резиносмешения. Здесь производят резиновую смесь на основе каучуков и связующих химических ингредиентов. Далее в камере резиносмесителя компоненты смешиваются до однородного состояния, превращаясь в огромные куски резины.
Те, в свою очередь, прокатываются через горячие вальцовочные станки, получаются широкие и длинные пластины. А из пластин этих уже вырезают заготовки разной формы для дальнейшей сборки обуви.
На Томском заводе обувь изготавливают клееную, формовую и литьевую. И это разные методы производства. Расскажем о них — как всегда коротко и понятно.
Клееная обувь
К клееной обуви относятся, например, традиционные азиатские галоши с малиновой байкой — «золотой стандарт» Томского завода.
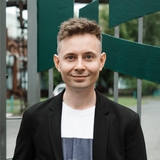
При производстве такой обуви пласты резины раскатывают до нужной толщины: для подошвы — одной толщины, для заготовок будущей обуви и деталей — другой. Обрезки, которые в производство не пошли, отправляются для повторного использования.
- Клееная резиновая обувь производится практически вручную на конвейере — и процесс напоминает сборку слоеного пирога: сотрудники последовательно накладывают на металлическую колодку текстильные и резиновые детали, которые уже обработаны клеем и мазью на основе натурального каучука;
- Далее заготовки покрываются лаком и отправляются в котел вулканизации — здесь под воздействием давления сжатого воздуха и высоких температур происходит процесс вулканизации, и резиновая смесь трансформируется в эластичную резину;
- После того, как обувь остыла, ее снимают с колодок, маркируют, упаковывают и отправляют покупателю.
Формовая обувь
В цехе формования производят резиновые сапоги общего и специального назначения.
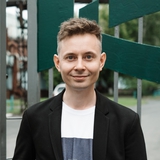
На мягкий дорн пресс-формы надевают чулок из трикотажа, на который последовательно накладывают голенище, полустельку на носок, передок, подошву и каблук. Для изготовления обуви спецназначения также дополнительно устанавливают ударозащитные подноски и антипрокольные стельки;
- Дорн со всеми собранными деталями вводят в пресс, где нагретые пресс-формы закрываются и под высокой температурой и давлением происходит процесс вулканизации. На каждый вид изделия есть свой температурный и временной режим. После того, как пресс-форма в прессе раскрывается, изделие снимается с сердечника.
- После остывания с изделия удаляют облой (излишки материала после формования) и резиновые сапоги готовы.
А за счет специальной рецептуры резиновых смесей обувь получает защитные свойства от воздействия агрессивных химических сред, неблагоприятных воздействий нефтепродуктов, жиров, масел и прочих.
Дизайнерские сапожки, флипперы и стильные галоши: литьевая обувь
У резины масса защитных свойств, лучший коэффициент трения с обледенелыми, мокрыми поверхностями.
Но производство такой обуви — это довольно трудоемкий процесс, требует значительное количество ресурсов
На заводе производят не только резиновую обувь, но и модели из ПВХ, ЭВА и полиуретана.
ЭВА (EVA) — сокращенное название от этиленвинилацетата. Это вспененный полимер с пористой структурой. Из него делают обувь (сапоги, сланцы, галоши), а еще коврики для машин.
У этого материала хорошая теплозащита, устойчивость к влаге, легкий вес. Но обувь из ЭВА плохо выдерживает механические повреждения.
ПУ (полиуретан) — это синтетический материал, который создают путем соединения нескольких полимеров. Процесс объединения образует вспененную структуру, в результате чего материал обладает упругостью, эластичностью и сравнительно небольшим весом. Сапоги из полиуретана хорошо держат тепло, защищают от воды, агрессивных сред, механических повреждений.
Из полиуретана производят высокотехнологичную многокомпонентную обувь в специальном исполнении, а также обувь для охоты, рыбалки и активного отдыха под собственным брендом — HARWELD
Томский завод резиновой обуви приобрел две литьевые машины ПУ полного цикла, сделанные под заказ — они позволяют выпускать высокотехнологичную комбинированную обувь. Это оборудование, по словам Дениса Игнатова, позволило выпускать обувь мирового уровня и значительно расширить модельный ряд выпускаемой продукции.
Многие модели, которые на нем выпускаются, запатентованы не только в России, но и за рубежом
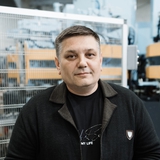
Здесь находятся флагманские станки предприятия. Для того, чтобы работать на такой машине, нужно соблюсти сложную процедуру подготовки компонентов. Внутри компьютера миллион папок: для каждой пресс-формы задаются свои настройки — разный размер подразумевает подачу разного объема материала и под разным давлением.
— Оборудование само организует процесс, выставляет нужные дозировки, следит за температурным режимом и в целом за всеми этапами производства обуви.
По периметру агрегата установлены пресс-формы, устройства для впрыска полиуретана и роботы-манипуляторы для обработки готовой обуви.
- Для создания полиуретановой обуви в швейном цехе делают специальные чулки из текстильного материала. Затем такой чулок надевается на металлический сердечник пресс-формы, создавая имитацию ноги внутри обуви;
- Далее устанавливается композитный подносок и антипрокольная стелька для специализированной обуви. Напоследок надевается деталь из вулканизованной резины для ходового слоя подошвы.
- Запускается автоматический цикл вращения карусельной установки. Пресс-форма закрывается, после чего последовательно и автоматически впрыскивается горячая смесь изоцианата и полиола, и в результате реакции образуется полиуретан, принимающий форму изделия.
Безотходное производство
У предприятия есть спецоборудование для переработки отходов производства и брака из резины в крошку мелкой фракции, эта крошка добавляется при изготовлении новой продукции. Это позволяет сделать производственный процесс безотходным, — отмечает Денис Игнатов, заместитель директора ТЗРО по маркетингу.
В год перерабатывается около 110 тонн отходов
На заводе также разрабатывается программа по приему использованной резиновой обуви в специальном исполнении для вторичной переработки. Так, предварительная договоренность о переработке б/у обуви достигнута с одним из клиентов завода — горнодобывающим предприятием из Кемеровской области.
Завод растет и развивается — и ему нужны новые активные и заинтересованные сотрудники. Свободных вакансий много, на сайте предприятия можно с ними ознакомиться.
Сайт предприятия: tzro.ru
Сайт бренда HARWELD (охота, рыбалка и активный отдых): harweld.ru
Фото: Михаил Новосёлов, ТЗРО